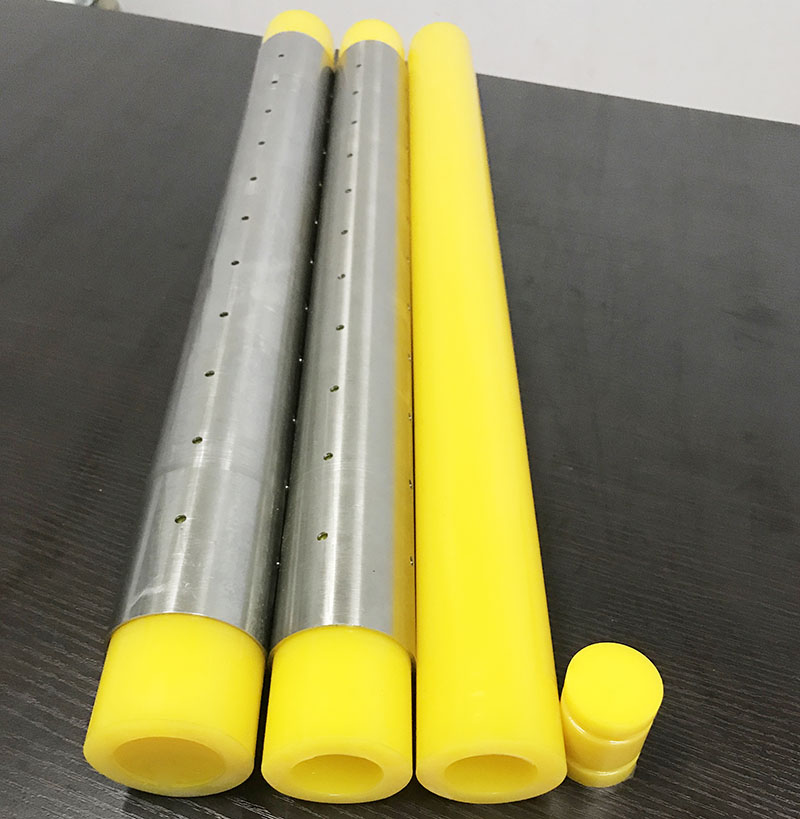
Dry-bag Isostatic Pressing Molds/Bags/Toolings
Categories: DIP mold-dry bag isostatic press
Application: Dry-bag Isostatic Pressing Molds/Bags/Toolings
InquiryMain description:
Dry-bag Isostatic Pressing Molds/Bags/Toolings
Dry-bag Isostatic Pressing Molds/Bags/Toolings
Dry-bag Isostatic Pressing Molds/Bags/Toolings
Dry bag isostatic pressing equipment is inseparable from isostatic pressing molds made of various polyurethane materials. In dry bag isostatic pressing, there are various molds for product molding, including molding molds for pressed rods, pipes and various special-shaped parts, as well as isolation packages in the press, all of which are made of special isostatic polyurethane. Made.
Different materials require different molding pressures, which generally need to be selected through practice or experience. For example, when pressing high-voltage electrical porcelain plastic materials, the optimal pressure is 100-120MPa, and when pressing zirconia and 95% alumina materials, the optimal pressure is 180-200MPa. The holding time is determined according to the cross-sectional area size of the blank, generally 0-5 minutes. For blanks with thick walls and large sizes, holding pressure can increase the plastic deformation of the particles, thereby increasing the density of the blank, generally by 2% - 3%, while making the density uniform inside and outside the blank. The pressure relief speed is a very important process parameter. If the pressure relief speed is not properly controlled, the green body may crack due to elastic aftereffects of the compact, elastic recovery of the plastic jacket, and gas expansion in the green compact. In the specific pressurization operation process, the pressure increase, pressure maintenance, and pressure relief processes should be based on factors such as powder characteristics, product shape and size, charging density, whether the packaged powder is degassed, and the thickness of the package wall. Decide.
After the blank is demoulded and pressed, the plastic jacket rebounds and separates from the blank. Due to the elastic aftereffect of the blank, the rigid core mold forms a gap of 0.2-0.3 mm between the blank and the core mold. Under normal circumstances, it can Smooth demoulding. During the demoulding operation, you should be careful and handle it with care to prevent collision and damage.
Blank Size and Performance Testing Whether the shape and size of the blank meet the requirements and the size of the cutting allowance of the blank depend on the structural design of the mold, the nature of the compact powder, the surface finish of the mold, the uniformity of powder filling in the mold cavity, Molding pressure, pressurization speed, jacket quality, compact cross-section size and compression ratio, etc. In cold isostatic pressing, it is difficult to keep these factors constant. Therefore, in order to ensure the shape and size of the product, a certain processing allowance is generally left. For molded bodies whose green strength is not high enough, they are easily damaged when used directly for cutting. The strength of the green body can be increased by bisque firing before cutting. The inspection of the blank is mainly to check whether there are layer cracks and cracks, whether the wall thickness is consistent, and whether there are any flaws, impurities and other defects on the surface.
We support all kinds of customization, if you need it, please contact us.
Phone/whatsapp:+86 18234744811
Email:sales@highindustryco.com