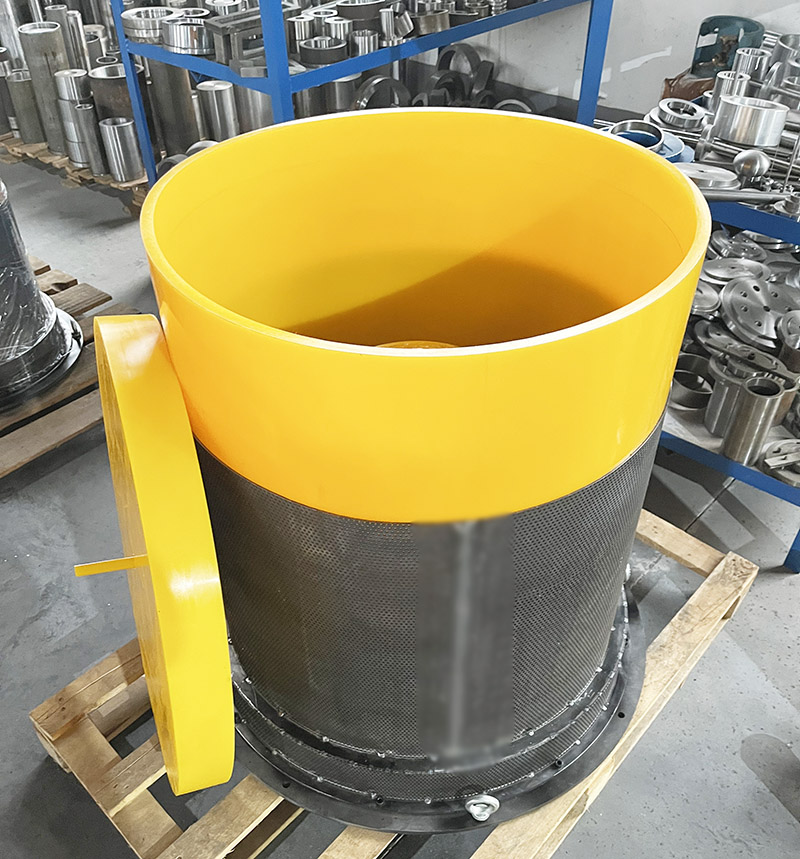
Introduction of CIP
Categories: CIP bags, CIP mold
Application: Introduction of CIP
InquiryMain description:
Introduction of CIP
Introduction of CIP
Introduction of CIP
Cold Isostatic Pressing (CIP) is a process widely used in various industries to create complex shapes from ceramic and metal powders. This innovative technique offers several advantages over traditional uniaxial pressing methods. By subjecting the powders to equal pressure from all directions, CIP ensures uniform density and eliminates defects that can occur during uniaxial pressing. The result is high-quality, homogeneous products with excellent mechanical properties. In this blog post, we will explore the methods, process, and applications of cold isostatic pressing, highlighting its significance in powder forming and its diverse range of uses across different industries.
Understanding Cold Isostatic Pressing
Explanation of Cold Isostatic Pressing (CIP)
Cold isostatic pressing (CIP) is a method of processing materials that involves compacting powders by enclosing them in an elastomer mold. The powders are then subjected to uniform pressure from all directions using a liquid medium such as water or oil. This pressure is applied at room temperature or slightly higher to obtain a "raw" part with sufficient strength for handling, processing, and further sintering. CIP is commonly used for plastics, graphite, powdered metallurgy, ceramics, sputtering targets, and other materials.
Description of CIP's Benefits over Uniaxial Pressing
CIP offers several benefits over uniaxial pressing, making it a preferred method for certain applications.
Greater Shape Capability: CIP allows for the formation of more complex shapes compared to uniaxial pressing. The pressure applied from all directions ensures greater uniformity of compaction, resulting in high-quality parts with intricate designs.
Reduced Distortion and Improved Accuracy: The use of an elastomer mold in CIP helps reduce distortion during the compacting process. This leads to improved accuracy in the final product, ensuring that the desired dimensions and tolerances are met.
Minimized Risk of Air Entrapment and Voids: By applying pressure uniformly from all directions, CIP helps minimize the risk of air entrapment and voids in the compacted material. This results in denser and more structurally sound parts.
Versatility in Material Types: CIP can be used with a wide range of materials, including plastics, graphite, ceramics, and powdered metals. This versatility makes it suitable for various industries, such as medical, aerospace, and automotive, where components with different material properties are required.
In summary, cold isostatic pressing offers a unique method for compacting powders and achieving high-quality parts with complex shapes. Its benefits over uniaxial pressing make it a valuable technique in industries that require precise and uniform compaction of materials.
Methods of Isostatic Pressing
Isostatic pressing is a powder processing technique that uses fluid pressure to compact a part. Unlike other processes that exert forces on the powder through an axis, isostatic pressing applies pressure uniformly from all directions. This method offers unique benefits for ceramic and refractory applications, allowing for precise tolerances and reducing the need for costly machining. There are two main methods of carrying out isostatic pressing: wet-bag and dry-bag isostatic pressing.
Description of wet-bag isostatic pressing
In wet-bag isostatic pressing, the powder is encased in a rubber sheath and immersed in a liquid that transmits pressure uniformly to the powder. The rubber mold, filled with ceramic or metal powder, is tightly sealed outside the pressure vessel. Once filled, the mold is submerged in the pressure fluid within the vessel, and isostatic pressure is applied to the external surface of the mold. This compresses the powder into a solid mass. Wet-bag technology is not as common as dry-bag isostatic pressing, but there are over 3000 wet bag presses used worldwide. These wet bags come in various sizes, ranging from 50mm to 2000mm in diameter. The wet-bag process can be relatively slow, taking anywhere from 5 to 30 minutes to process material. However, advancements in high-volume pumps and loading mechanisms have helped to speed up the process.
Description of dry-bag isostatic pressing
In dry-bag isostatic pressing, the tooling itself is built with internal channels into which high-pressure fluid is pumped. Rather than immersing the tooling in a fluid, the fluid is pumped directly into the channels within the tooling. This method eliminates the need for a separate rubber sheath and the immersion step. Dry-bag isostatic pressing is well-suited for automation and can be used for pressing relatively long runs of compacts at high production rates. The powder is added to the mold, the mold is sealed, pressure is applied, and then the part is ejected. The integrated mold in this process makes automation easier compared to wet-bag isostatic pressing.
CIP Molds /Bags for Ceramics, metal and more powders molding
We support all kinds of customization, if you need it, please contact us.
Phone/whatsapp:+86 18234744811
Email:sales@highindustryco.com