The Isostatic Pressing Polyurethane Molds/Bags for Isostatic Pressing Process
The physical nature of the hydrostatic process is to use the Basseger principle, the fluid is basically incompressible, the pressure is applied to the fluid, the pressure is transmitted continuously through the fluid, and the pressure is equal everywhere in the liquid. However, it should be noted that the liquid will also shrink under high pressure, and it is generally believed that when the pressure exceeds 50MPa, the volume will shrink significantly, up to a quarter.
The high-pressure cylinder made of large high-strength steel forgings is the main part of the isostatic press, or the cylinder is lined with steel parts, and the outside is wrapped with steel tape and steel wire to improve the compressive strength of the press cylinder and ensure the safety of the press cylinder. The high pressure cylinder is filled with liquid oil, or the emulsion containing 5% oil, or pure water, and these liquids are used as the medium for transferring pressure. During operation, a high pressure pump is used to add a little liquid to the pressure cylinder, which can increase the liquid pressure in the cylinder to about 200MPa. The powder that needs to be pressed is packed in a flexible plastic sleeve (bag), the air in the rubber sleeve is drained, and the plastic bag is sealed to prevent oil from entering the sleeve during the pressing process. The rubber sleeve is placed in the liquid medium in the high pressure cylinder. Under the action of the high pressure liquid, the powder in the rubber sleeve is pressed into a compact. Usually, a steel jacket of the same size and shape is set on the outside of the flexible plastic sleeve to ensure the accuracy of the shape and size of the compact. Flexible with natural rubber or artificial plastic manufacturing, usually the composition of artificial plastic (mass fraction) is: polyvinyl chloride resin 100 parts, dioctyl phthalate 100 parts (or dibutyl phthalate), terylene lead sulfate 2 to 3 parts, plus stearic acid 0.3 parts, stirring mixed evenly, after vacuum exhaust, with mixed tuned colloidal manufacturing soft cover process is: Only put the mandrel that meets the design size requirements in the mixed liquid glue, so that the surface of the mandrel is coated with a certain thickness of colloidal, and then put the mandrel with colloidal in the appropriate high temperature oven for a certain time, water cooling release after the sleeve is set, and carefully check to ensure that the rubber sleeve does not leak, otherwise, when pressurizing the high-pressure cylinder of the isostatic press, The liquid penetrates into the sleeve and the powder becomes a thin metal mud and cannot be formed.
The flexible sleeve containing powder is placed into the liquid of the high pressure cylinder, and the soft mold sleeve and powder are simultaneously compressed and deformed. Different from the steel die pressing, the soft die sleeve and the pressed powder are deformed at the same time during isostatic pressing, eliminating the friction pressure loss between the die and the powder, and the relative motion distance between the powder is very small, especially the longitudinal is much smaller than the transverse. The hydrostatic pressure of the liquid in the high-pressure cylinder is considered to be equal. In this way, the density of the isostatic pressed powder compact is approximately equal everywhere.
The Isostatic Pressing Polyurethane Molds/Bags for Isostatic Pressing Process
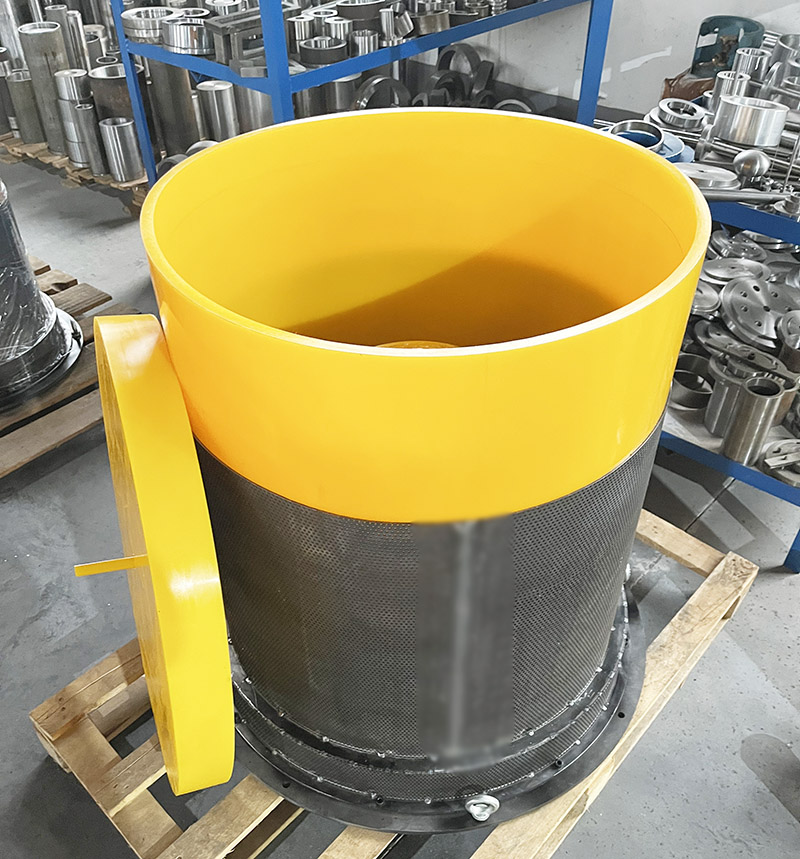
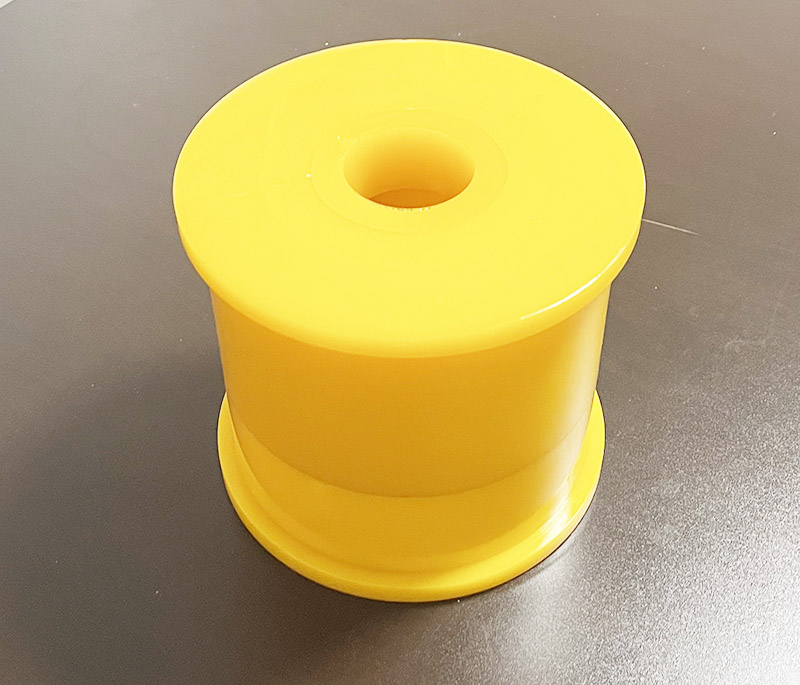
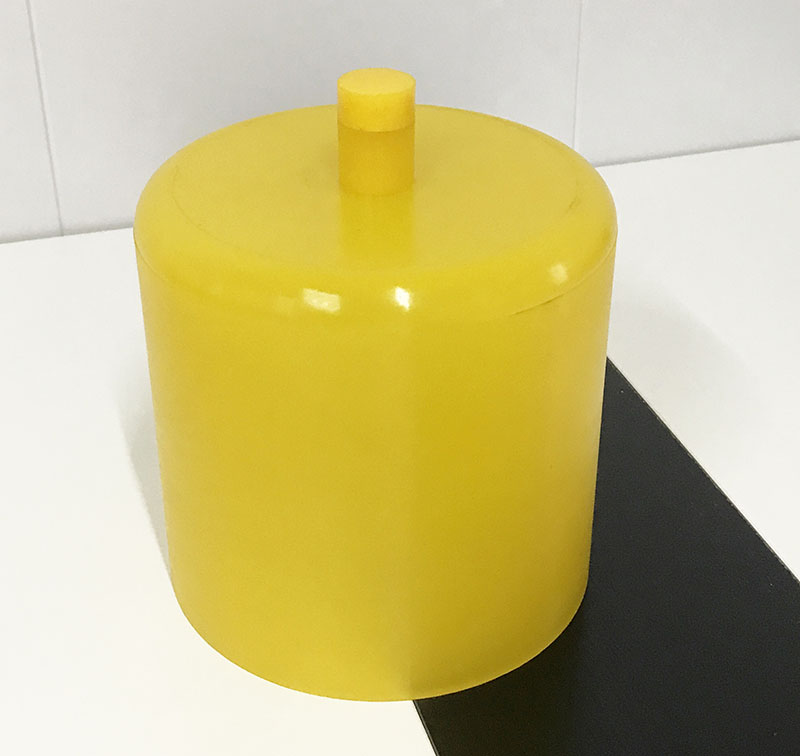

We support all kinds of customization, if you need it, please contact us.
Phone/whatsapp:+86 18234744811
Email:sales@highindustryco.com
Polyurethane Products Pu Products Rubber Mold Plastic Mold