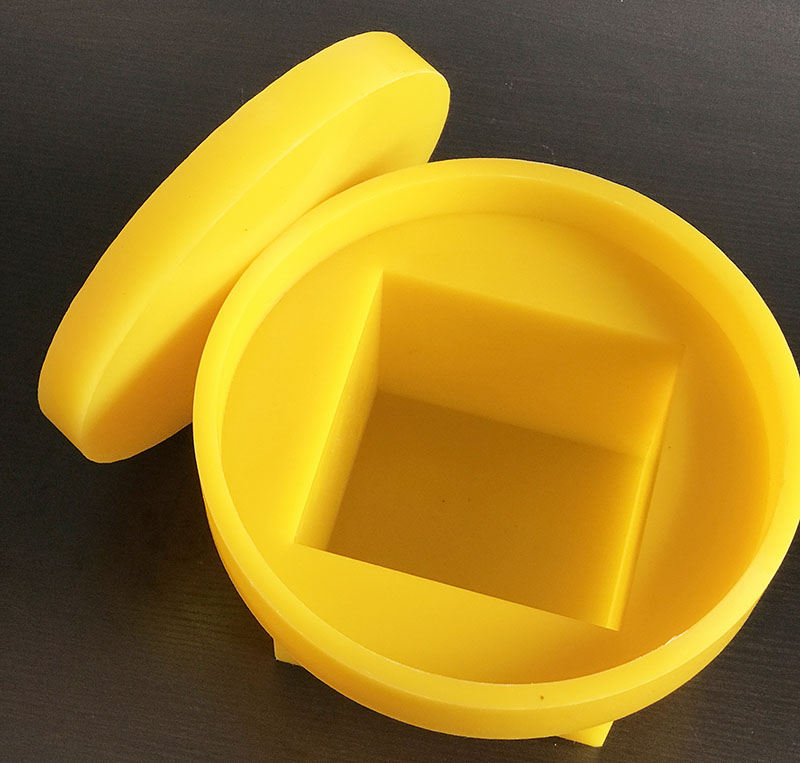
Polyurethane Isostatic Pressing Molds/ Bags
Categories: Powder metallurgy bag mold
Application: Polyurethane Isostatic Pressing Molds/ Bags
InquiryMain description:
Polyurethane Isostatic Pressing Molds/ Bags
Polyurethane Isostatic Pressing Molds/ Bags
Polyurethane Isostatic Pressing Molds/ Bags
The polyurethane polymer material specially developed for isostatic pressing molds has the characteristics of good plasticity, good elasticity, good oil resistance, water resistance and oxidation aging resistance. Embodied in isostatic pressing production, it means precise molding, smooth surface and long service life. According to the usage, there are targeted solutions, including design, manufacturing of rubber sleeves, tooling, lifting and other fixtures. Of course, the so-called isostatic pressing molds that are crudely manufactured by ordinary polyurethane products companies with conventional polyurethane materials cannot realize those advantages. After the powder filling is completed, the charging port is sealed with an end plug, some use varnish as the adhesive to seal, or no adhesive is required, and it is best to use elastic bands for external bundling, so that during the compression deformation of the end plug , still has the function of fastening and sealing, and will not fall off. It is also effective to use iron wire to bind. In order to improve the quality of the green compact, some products are larger in size. Before the sheath is sealed, a sponge pad or filter paper for filtering is placed between the powder and the end plug to prevent the powder from being taken away during pumping, such as using rubber The cover of the end plug can be inserted into the sponge pad through the rubber plug with the medical injection tube. The other end of the injection needle tube is connected with the vacuum system, which can realize the degassing of the powder in the cover. After the injection needle tube is taken out, the rubber stopper can Self-sealing, the easiest degassing device. The sheathing mold and supporting attachments are easy to be dirty when the powder is loaded into the mould, and should be cleaned well to avoid bringing powder and dust into the high-pressure cylinder. If the cleaning is not clean, the powder will be brought into the medium in the cylinder. When the pressure is released under high pressure, these solid particles have high energy, which is easy to cause erosion damage to the high-pressure seals of the hydraulic system. For this reason, the outside of the jacket mold before entering the cylinder must be cleaned, and the liquid medium in the high-pressure cylinder must be replaced regularly.
In order to ensure the shape and size of the product, in general, a certain machining allowance is left. Because the strength of the green body is not high enough, it is easy to be damaged when it is directly used for cutting. Usually, biscuit firing is used to improve the strength of the green body, and the precise shape and size required for re-cutting, and there is a margin for firing shrinkage and grinding of the ceramic body. .
In the cold isostatic pressing molding technology, according to the different molding methods, the casing and the mold are divided into the casing mold used in the wet bag method, the dry bag method, and the balanced pressing method. No matter what kind of mold, it is composed of four basic components: plastic mold, rigid mold, port sealing device and supporting device.
The cover, end plug and mold pad of Hi Industry solid mold are made of special polymer materials. In cold isostatic pressing, the plastic mold not only plays the role of mold, but also plays the role of transmitting pressure to make the powder compact. The mold core, mold, etc. of the rigid mold are made of metal materials. The size and shape of the rigid mold remain unchanged during the molding process.
In the design of cold isostatic pressing molds in normal mass production, there are usually the following steps:
(1) Carry out small-scale simulation tests to determine the compression ratio during powder molding. The relationship between pressure and properties such as compact density and strength, and the basic data such as the shrinkage rate of the blank after sintering.
(2) According to the obtained test data. And consider the machining allowance and dimensional tolerances that need to be left after forming. Design the shape and size of the mold, and then check it through the actual measurement results. After repeated tests for many times until the shape, size and performance of the formed blank meet the technical requirements.
(3) Select the jacket material, determine the wall thickness of the jacket and the material of the metal core mold, and determine the assembly method of the mold, the sealing of the charging port and the port, and the fixing device. If there is practical experience and data of this work, the design steps can be simplified. In short, in the design of the mold, we should not only pay attention to the rationality of the design, but also take into account the economical practicability of the mold.
The main factors affecting the package and mold design are as follows:
There are a series of factors to consider in jacket and mold design, among which the packing density of powder is the most critical. The uniformity of the filling density of the material in the mold and the size of the filling density are the main basis for the mold design.
We support all kinds of customization, if you need it, please contact us.
Phone/whatsapp:+86 18234744811
Email:sales@highindustryco.com