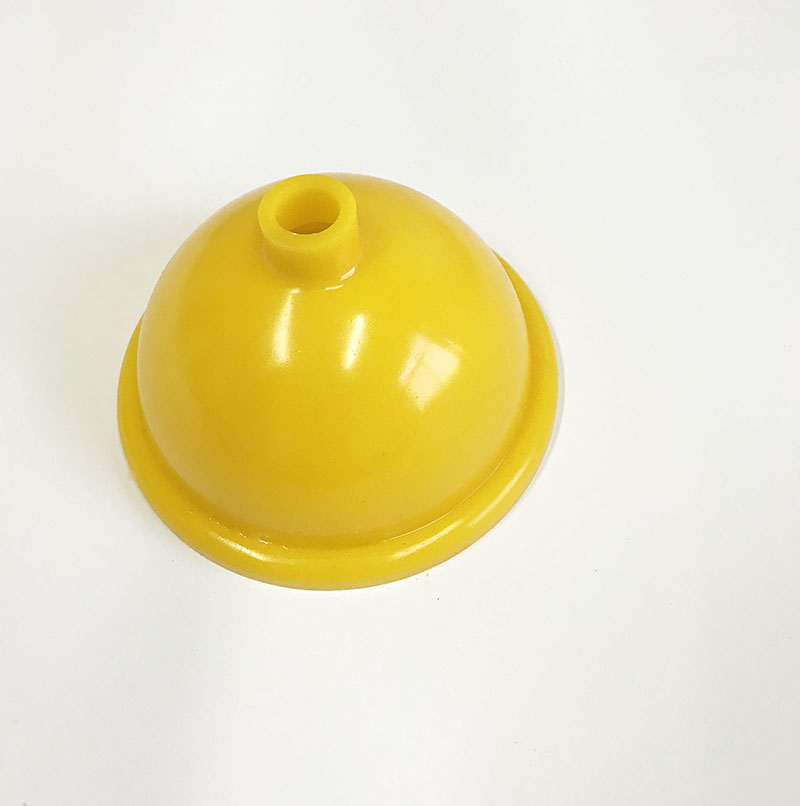
Isostatic Pressing Molds for Ceramic
Categories: CIP powder forming bag mold
Application: Isostatic Pressing Molds for Ceramic
InquiryMain description:
Isostatic Pressing Molds for Ceramic
Isostatic Pressing Molds for Ceramic
Isostatic Pressing Molds for Ceramic
The production of wear-resistant ceramics needs to go through multiple technological processes such as powder making, grinding, compacting, sintering, and cutting, among which compacting is a very important core link. In the past, we mainly used dry pressing to form compacts, but now the maturity of isostatic pressing technology has brought new breakthroughs in the production of wear-resistant ceramics.
The isostatic pressing technology is to wrap the green body to be pressed with an elastic mold, then put it into a closed high-pressure cavity, and apply ultra-high pressure to press the green body.
From the perspective of space, the pressure provided by the isostatic pressing technology is exactly the same in all directions, and from the perspective of time, the pressure on the green body during the pressing process also remains unchanged. Such characteristics make the pressed body high density, good strength, uniform compactness, excellent mechanical properties and easy machining.
Isostatic pressing technology is used in the production of wear-resistant ceramics, which also improves the performance of wear-resistant ceramic products.
1. The wear-resistant ceramics produced by isostatic pressing technology have high density and good compactness, and the strength and wear resistance can be increased by 20%.
2. Isostatic pressing technology can produce wear-resistant ceramic body with large size and complex shape by controlling pressure and elastic mold.
3. The density of the wear-resistant ceramic body produced by isostatic pressing technology is consistent in all directions, and the deformation of the sintered product is small. Moreover, the internal stress of the green body is small, and it is not easy to break and delaminate, which greatly improves the quality of the green body.
But while the advantages are obvious, the isostatic pressing technology also shows some disadvantages in the production of wear-resistant ceramics.
The isostatic pressing technology is relatively complicated, the precision of the green body produced is low, the surface is relatively rough, and further processing and grinding are required, and the production efficiency is low.
In the actual production of wear-resistant ceramics, we can comprehensively consider the size, precision, wear-resistant performance requirements, quantity and quality of the product, and choose the appropriate compaction method, or combine the two, first use dry pressing, and then use isostatic pressing to produce high-quality wear-resistant ceramic blanks.
The isostatic pressing molds samples for ceramic
We support all kinds of customization, if you need it, please contact us.
Phone/whatsapp:+86 18234744811
Email:sales@highindustryco.com