Isostatic Pressing ITO molds
ITO is the English abbreviation of indium tin oxide. It is characterized by high resistivity and light transmittance, so ITO targets are very suitable for making solar cells, displays and conductive glass. In the field of liquid crystal display, the screen is getting bigger and bigger, and the color requirements are getting higher and higher, so the development of ITO is very important. The forming process determines the quality of the ITO target. ITO target forming technology can basically be divided into two types: dry method and wet method. The advantage of the dry method is that it is easy to produce, does not need to be dried, and is formed by pressure. Wet forming requires the mixing of various forms of objects for reaction, followed by drying, and the size of the produced targets is relatively large.
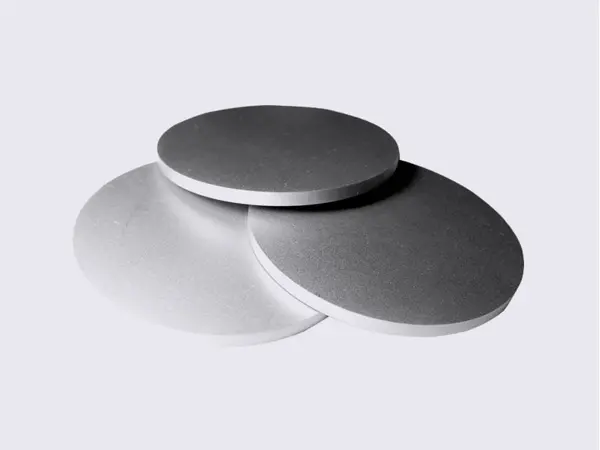
1. Dry forming process
1.1 Cold isostatic pressing
The cold isostatic pressing process needs to be carried out at room temperature, and the ITO powder is placed in a high-pressure container in proportion, because the liquid will not be compressed, so the pressure applied to the liquid will be evenly distributed in all directions, and the formed embryo body The density will be relatively uniform. Its disadvantage is that if the force is uneven for some irregularly shaped and large-sized targets, the target may break and cause worker poisoning. There are corresponding solutions to the above problems.
After the cold isostatic pressing of the ITO powder, the N-level pressure relief protection is used when the pressure is released, so as to ensure the uniformity of the target density and produce the ITO film. Another solution is to add water, acetone, and absolute ethanol to the ITO powder, and then put it into a ball mill tank for ball milling and sieving operation, pre-dry pressing in a steel grinding tool, and then perform cold isostatic pressing . This operation can greatly reduce the risk of poisoning. The forming of large-sized targets can be completed by putting the ITO slurry into a high-frequency vibrating abrasive to dry the green body, and then perform the same cold isostatic pressing process.
1.2 Stamping
Stamping, as the name implies, is to put the blank into the abrasive tool, and then apply pressure to the abrasive tool to deform it to a certain shape and size. The advantage of this process is that workpieces of various shapes can be produced, and the size is very precise, and it can be mass-produced by using automation technology. However, this method is rarely used, because the target is easy to crack during production. A person from Japan added polyvinyl alcohol to ITO, sieved it and added it to a stamping mold, and sintered it after forming to obtain a target with a density of 99.2%. Not easy to crack.
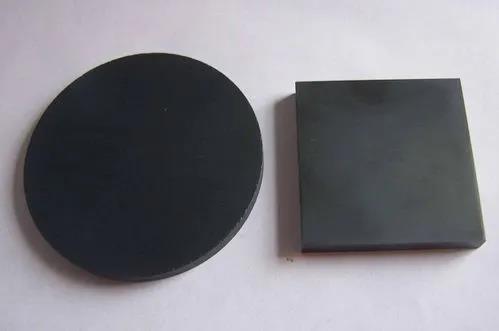
2. Wet forming process
2.1 Extrusion
The process of mixing powders, lubricants and binders with water, putting the plastic into a mold, and applying pressure to shape the material is known as extrusion. Extrusion molding is often used to make fireproof materials such as furnace tubes and sheath tubes, and is also used in the production of some electronic materials. Recently, it is also used in the production of ITO targets. Add ITO raw materials of different particle sizes in proportion to deionized water, polyethylene glycol and binder polyvinyl alcohol to ball mill and sieve, extrude the blank under the action of external pressure, roll and degrease under a certain temperature condition , and then sintered to obtain a high-density ITO target. This kind of target has low strength, and the blank is prone to cracks and pits on the surface, so this process is not very commonly used in the production of ITO targets.
2.2 Gel injection molding
The basis of gel injection molding is to configure the slurry, and the requirements for the slurry are viscosity and high solid phase. The monomers in the slurry are then combined to consolidate the slurry, which produces a green body with high density and high uniformity. Gel injection molding is easy to operate and low cost, and the additives are all substances, so there will be no impurities after sintering. The emergence of this technology is due to the combination of ceramic forming and polymer chemistry. This process is mostly used in the production of component ceramics, porous ceramics and gradient ceramics. The targets produced by this technology have high stability and good uniformity, and targets with complex shapes and large sizes can be produced. Mix the ITO raw material with the monomer, dispersant, initiator, bonding agent and water for ball milling to make a suspension. When the suspension is put into the grinding tool, a gel reaction will occur, and the final ITO powder will be in situ Wrap and solidify to form a flexible three-dimensional network structure to obtain a green body, which will be sintered after drying to obtain a high-density target. Because the green body of the slurry with high solid content has high density and high strength, it is not easy to crack or deform, so high solid content can produce high-density ITO targets. In order to solve the size problem, large-sized target blanks can be made by adding slow-release agents and plasticizers on the above basis.
The water-soluble epoxy resin added to the ITO raw material is used as a forming agent after ball milling and then solidified. After sintering, a target with high density and relatively high resistivity can also be obtained. This can greatly reduce the erosion of toxic gas to the air during gel injection molding, and also protect the safety of the staff.
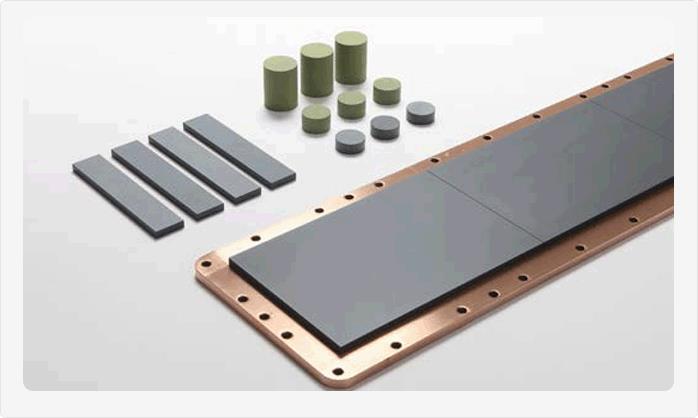
Jiangsu High Industry on the research and development and production of high-performance polyurethane isostatic pressing molds. Through in-depth cooperation with many isostatic pressing equipment manufacturers and in-depth study of the industry, the developed isostatic pressing polyurethane mold series products have the characteristics of long service life, high precision, small deformation, easy demoulding, etc., and are widely used in ceramics, etc. Static pressing mould, cemented carbide isostatic pressing mould, rare earth permanent magnet material isostatic pressing mould, graphite isostatic pressing mould, etc.
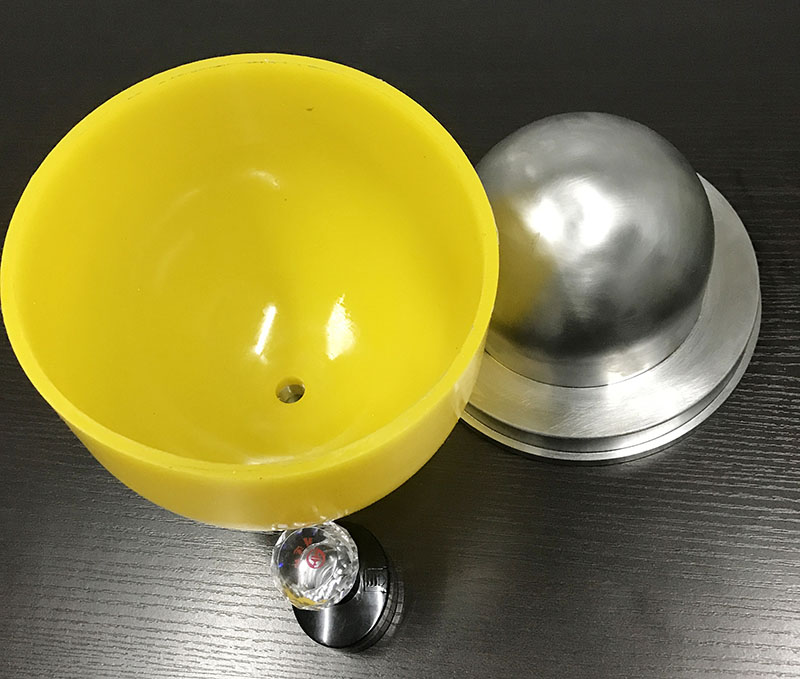
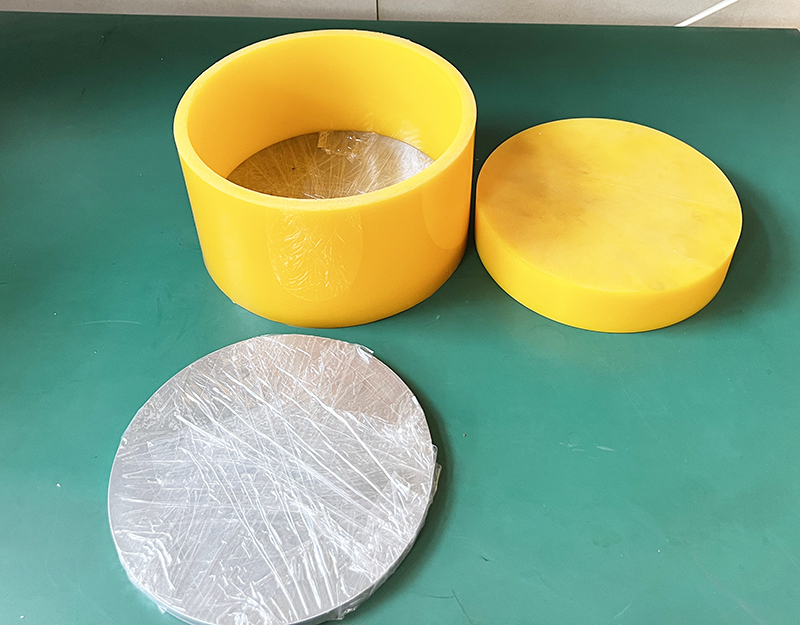
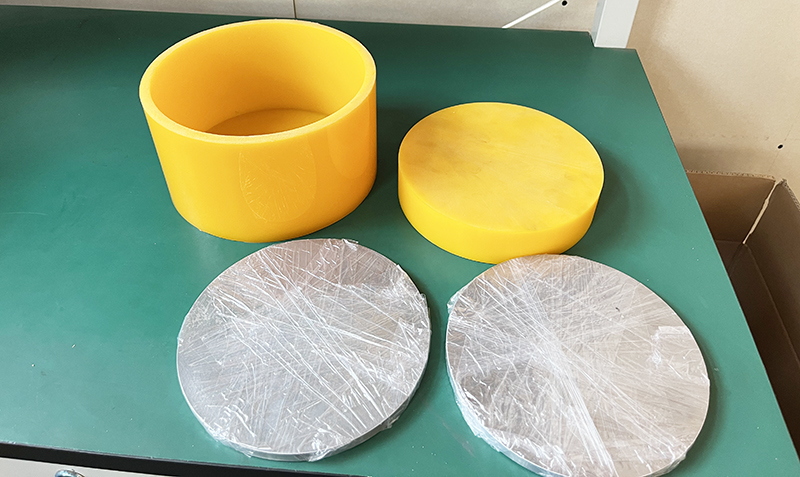
We support all kinds of customization, if you need it, please contact us.
Phone/whatsapp:+86 18234744811
Email:sales@highindustryco.com
Rubber Mold Plastic Mold Polyurethane Products Pu Products