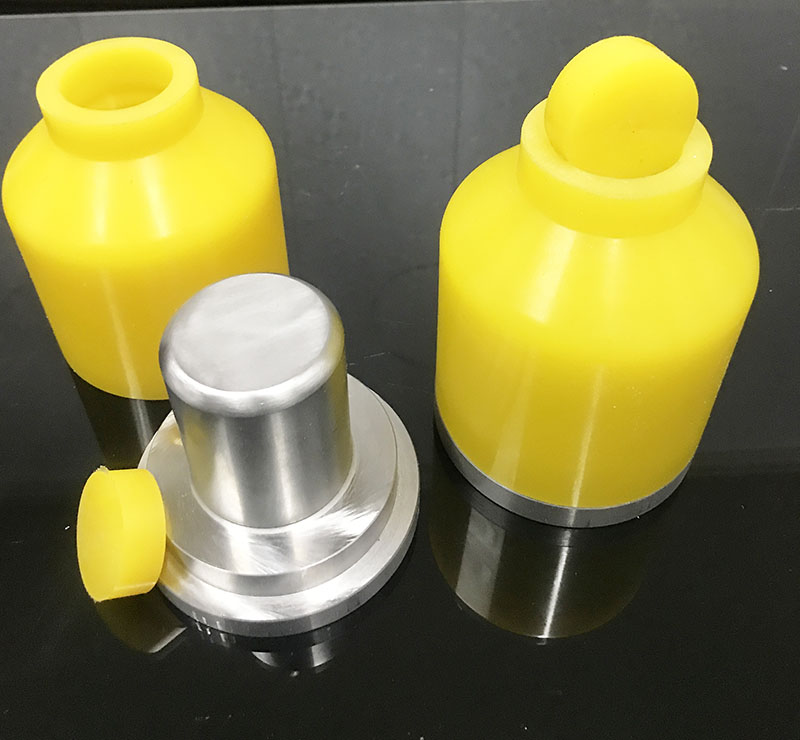
CIP- Cold Isostatic Pressing
Categories: CIP bags, CIP mold
Application: CIP- Cold Isostatic Pressing
InquiryMain description:
CIP- Cold Isostatic Pressing
CIP- Cold Isostatic Pressing
CIP- Cold Isostatic Pressing
Dry bag cold isostatic pressing techniques apply liquid materials (such as water or oil or ethylene glycol mixed in liquid) to apply pressure to the powder form. The powder is placed in a mold with a fixed and immovable form, so that the mold can avoid liquid penetration into the powder. For metal materials, the cold isostatic pressing technique can achieve about 100% of the basic theoretical relative density, while the more difficult to shrink porcelain powder can achieve about 95% of the basic theoretical relative density.
Very high working pressure causes the gap in powder to shrink and even fade. Under high pressure, metal powder causes deformation because of its plasticity. Porcelain powder is likely to be slightly crushed, the relative density is improved, and then the "embryo" parts can be solved, produced, processed and roasted. Typical working pressure range is 100-600MPa, the temperature is usually indoor temperature, if higher temperature is needed, the heat exchanger can be raised to about 93℃. It is not known that the temperature will rise when the water is reduced, and every 100MPa increase will increase by about 4℃, so the risk of boiling at a higher temperature will increase with it.
The common use of cold isostatic pressing includes porcelain powder soil, high purity graphite, refractory thermal insulation materials, electrical insulation, and its reduction of high porcelain. Raw materials include silicon nitride, carbon carbon composite material, boron carbide, boron carbide, titanium boride, cuspate, etc. The technology has been extended to new applications, such as sputtering targets, coatings on valve components used to reduce cylinder damage in automotive engines, telecommunications networks, electronic components, aerospace and automotive industries.
Dry bag cold isostatic pressing technology has the following advantages: improve the soil level of the product, improve the physical performance of the product, the relative centralization of the data information in the production and manufacturing stage, can safely manipulate the production and manufacturing, low corrosion, high efficiency and low cost.
The whole process of relieving pressure in cold isostatic pressing process also determines the quality of "embryonic" steel cutting. Because the metal material or porcelain powder is compacted, the vapor body is trapped in the middle of the particulate matter, and the gas pressure increases with the increase of external working pressure in the production process. The metal block has very high strength and plasticity, after the cold isostatic pressure step, will naturally release the gas into.
As everyone knows, because porcelain "embryo" steel cutting is more brittle, if the working pressure has been released too quickly and efficiently and uncontrollably, porcelain steel cutting is likely to crack in the area where the gas can not escape. Preventing such a thing takes the form of adjusting the pressure relief system software to release the increased working pressure in a controllable way, which is especially critical at lower pressures, when the increased working pressure is equivalent to the internal air pressure, and the trapped gas will directly affect the thermal stress.
We support all kinds of customization, if you need it, please contact us.
Phone/whatsapp:+86 18234744811
Email:sales@highindustryco.com