Isostatic Pressing
Isostatic pressing (isostatic pressing, IP) is the role of high-pressure pump to the fluid medium (gas or liquid) pressed into a high-pressure steel sealed container, the static pressure of the high-pressure fluid acts directly on the powder in the elastic mold sleeve, the powder body in the same time in all directions and balanced pressure to obtain a uniform density distribution and higher strength of the press bad. The world's first isostatic press in 1939 in Sweden was developed successfully. The significant advantage of isostatic forming is to be able to press the complex shape of the pressed parts, and uniform density distribution, high strength, the pressing pressure is lower than the steel die pressing method. Usually, isostatic forming according to its characteristics into cold isostatic pressing and hot isostatic pressing, the former commonly used water or oil as the pressure medium, so there is liquid hydrostatic pressure, hydrostatic pressure or oil hydrostatic pressure; the latter commonly used gas (such as argon) as the pressure medium, so there is a gas hot isostatic pressing.
1. Cold isostatic pressing
Cold isostatic pressing into the development of technology and process of metal powder cold isostatic pressing technology (cold isostatic pressing, CIP) by Westinghouse LampCompany's Madden invented in 1913, was used to prepare tungsten, molybdenum wire blanks, the technology is still used in the refractory metal industry. The dry bag cold isostatic pressing technology for semi-automated production of ceramic parts was invented by Jeffrey of ChampionSpark Plug in 1942. In World War II, CIP technology was extended to the pressing of explosives, nets, and other protective materials, and after World War II, a larger capacity and higher ability to withstand the force of the container was manufactured to press metal and ceramic powder materials. 610mm, 2450mm long, and 551MPa press was used for the pressing of powder. The press is used for the pressing of beryllium powder, and a large part of metal powder art and parts are produced by cold isostatic forming as the main step in the production of WeiYi, including tungsten, molybdenum, beryllium, tantalum, tungsten carbide/cobalt table gold, P/M high speed steel, P/M composite materials, etc. The pressing pressure can vary from 200-400MP. with special ones reaching 760MPa, and the powder body inside the elastomer jacket is pressed from 55%~65% of the theoretical density to 75%~85% of the theoretical density by CIPOW. Cold isostatic pressing can be used as the top densification step of hot isostatic pressing, after sintering, it can also be forged, extruded, rolled, stamped and hot isostatic pressing.
2. Hot isostatic pressing
The United States Bttelle Institute in 1955 to develop hot isostatic technology (hot isostatic presin, HIP), first used in the atomic energy reaction process fuel components of the diffusion bonding, so then known as pneumatic bonding. In 1963, Sweden ASEA company with pre-stressed steel wire winding structure to manufacture HIP equipment, the main structure of a high pressure vessel, its compact structure, safe and reliable, laid the foundation for the vigorous development of HIP technology. ) in the isostatic high-pressure vessel at the same time by the combined effect of high temperature and high pressure, strengthening the pressing and sintering process, reducing the sintering temperature of the product, reducing the range of 10% ~ 159 6 above, and make the treated material still maintain the fine grain crystal structure, thus showing the advantages of HIP technology in powder metallurgy and ceramic materials sintering. The three process parameters of temperature, pressure and time can be adjusted and controlled during the hot isostatic pressing process, which can effectively eliminate the residual trace porosity inside the product and improve the relative density of the product. Many metal and non-metal powders have been sintered by HIP method to obtain products and materials close to theoretical density values.
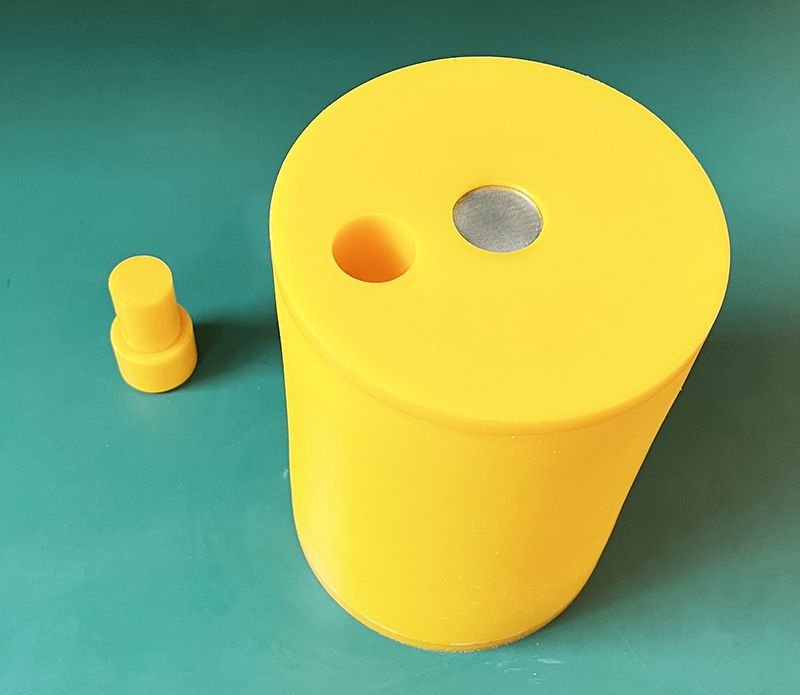

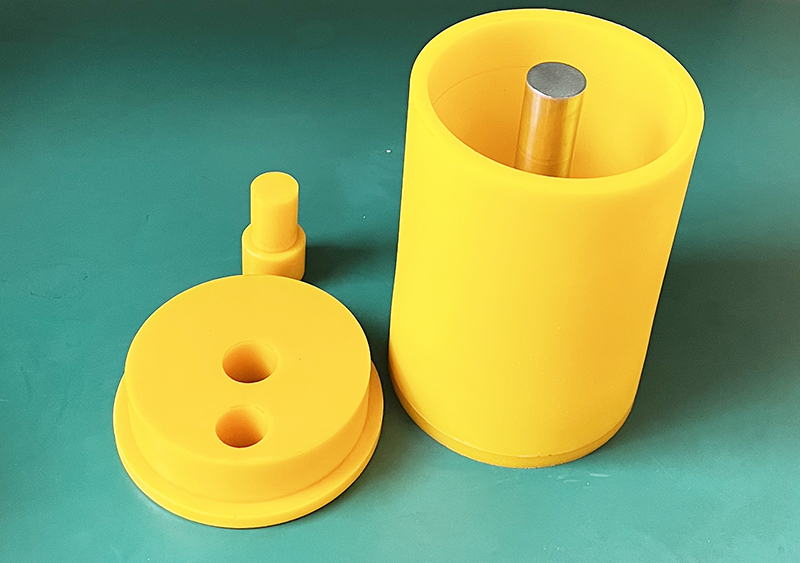
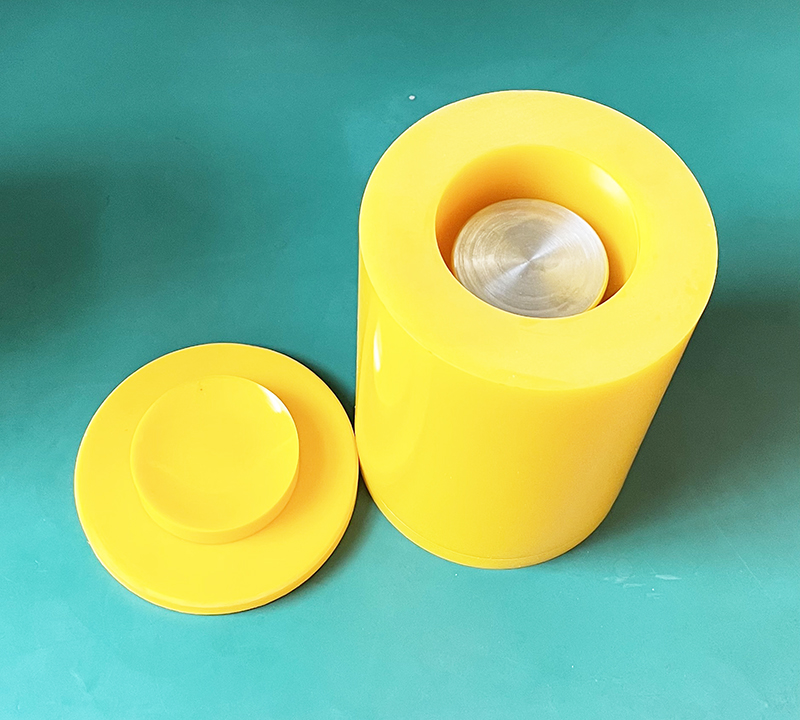