Introduction to Cold Isostatic Pressure Technology
Cold isostatic pressing technique uses a liquid medium (such as water or oil or glycol mixed liquid) to apply pressure to the powder. The powder is placed in a fixed shape mold, which prevents the liquid from penetrating the powder. For metals, cold isostatic pressing techniques can achieve a theoretical density of about 100%, while more difficult to compress ceramic powders can achieve a theoretical density of about 95%.
Common applications for cold isostatic pressing include the consolidation of ceramic powders, graphite, refractory materials, electrical insulators, and the compression of advanced ceramics. Materials include silicon nitride, silicon carbide, boron nitride, boron carbide, titanium boride, spinel, etc. The technology is expanding into new applications such as the compression of sputtering targets, the coating of valve components used to reduce cylinder wear in engines, telecommunications, electronics, aerospace, and automotive applications.
Cold isostatic pressing technology has the following advantages: improved consolidation of the product, increased mechanical properties of the product, relatively centralized data in the production chain for safer production control, very low corrosion, high efficiency and low cost.
The decompression process in the cold isostatic pressing process also determines the quality of the "raw" briquettes. As the metal or ceramic powder is compacted, the gas is trapped between the particles and the pressure increases with the external pressure applied during the process. Metal briquettes are very strong and ductile, and the entrained air is naturally released after the cold isostatic pressing process.
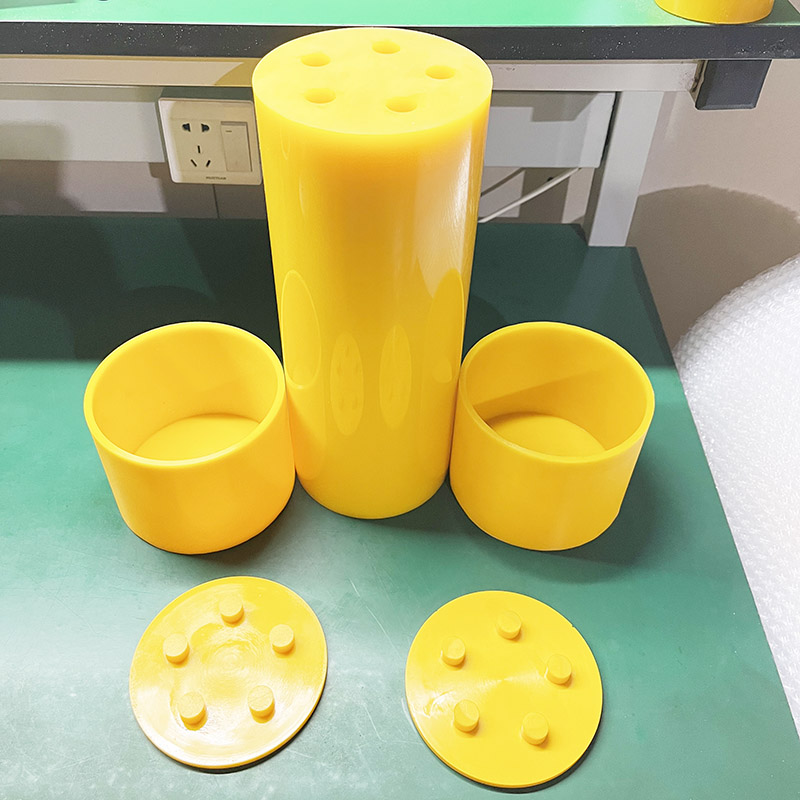
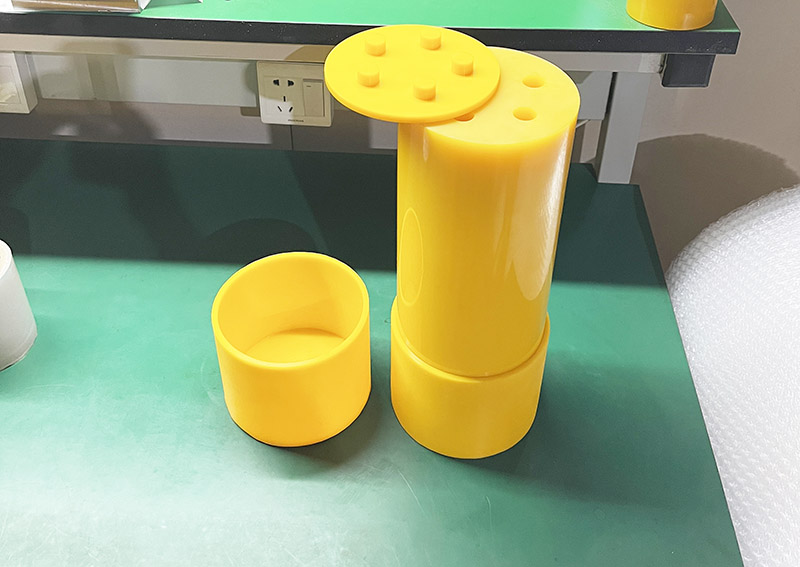
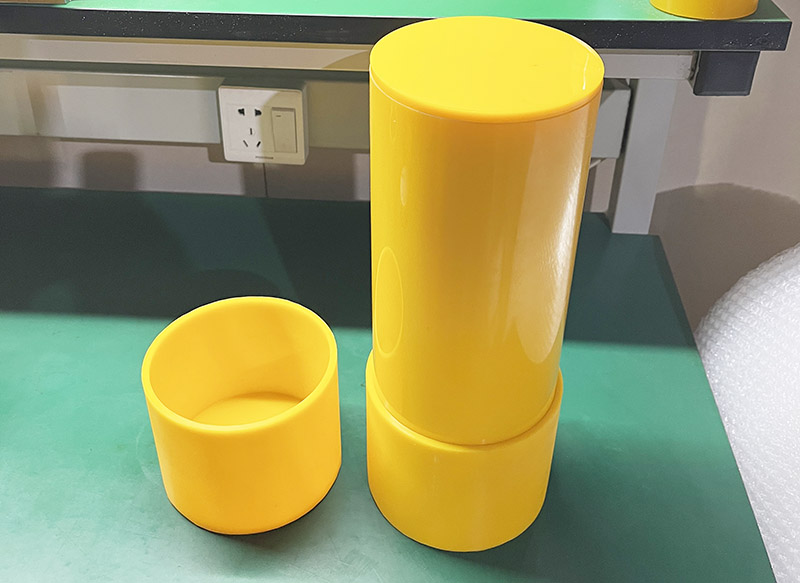
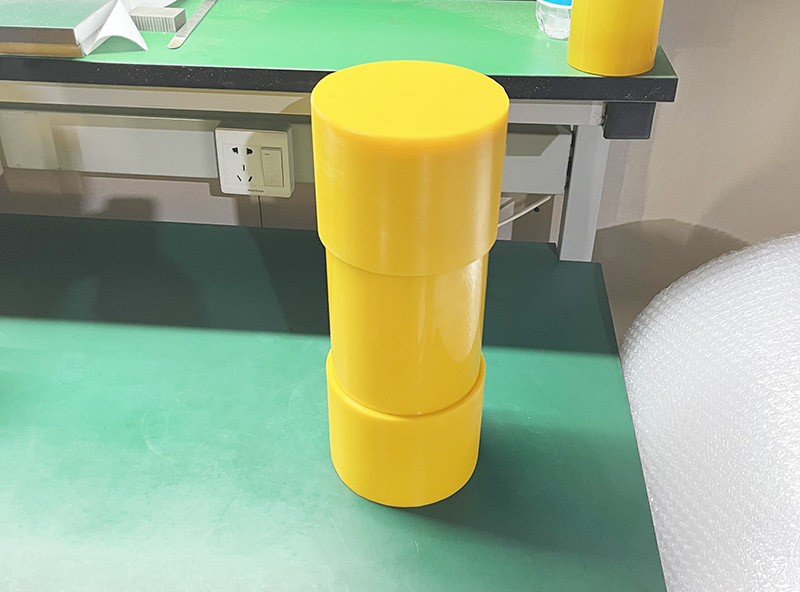