Wet-bag Isostatic Pressing and Dry-bag Isostatic Pressing
The wet bag isostatic pressing process is a versatile option for achieving high compact densities from metal and ceramic powders. A common shape for this type of pressing is an axisymmetric open or closed end, hollow shape, such as a tube. The geometry and volume of the mold cavity are designed to achieve a target final dimension. The inner diameter of such a pressed shape would have higher precision than the outer diameter. Another option is a dilating tool that has the pressurized fluid accessing the inner surface of the object; powder is pressed outward from an inner elastomeric mold wall against an outer rigid casing. The process provides a means to produce high and uniform pressure and high compact density due to the elimination of die wall friction. Enhanced density is only one feature of interest. Perhaps more important is the access to much different shapes than are possible with uniaxial pressing.
Dry bag isostatic pressing is an efficient production method for small parts with axisymmetric shapes. It is used to produce high-quality ceramic bodies for spark plugs. Since the rubber tooling is integrated into the apparatus, separate immersion and removal steps are not needed, which leads to ease in automation and fast production rates. However, there is friction on the side of the mold that does not experience compression from the pressurizing liquid. Likewise there are more shape and size limitations in the dry bag process. For example, spark plugs require green machining to develop the surface features needed.
Advantages and Disadvantages. Isostatic pressing is frequently chosen to achieve high compact densities and also to access shapes that cannot be compacted in uniaxial presses. Somewhat complex shapes can be engineered into the elastomeric molds if desired. The wet bag variation is better suited to production of large parts as compared to the dry bag process. However, loading and unloading of the molds decreases the productivity and limits the automation for wet bag pressing. Likewise somewhat higher densities are possible with wet bag processes as they involve very little friction. The dry bag version has the edge on automation and production rate. For both types of isostatic pressing, the tooling cost and complexity of the process are higher than for uniaxial pressing.
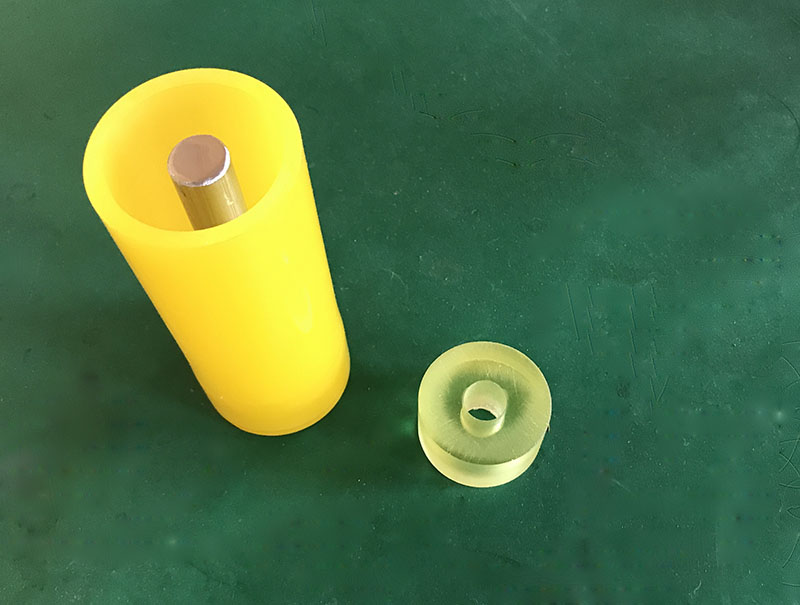
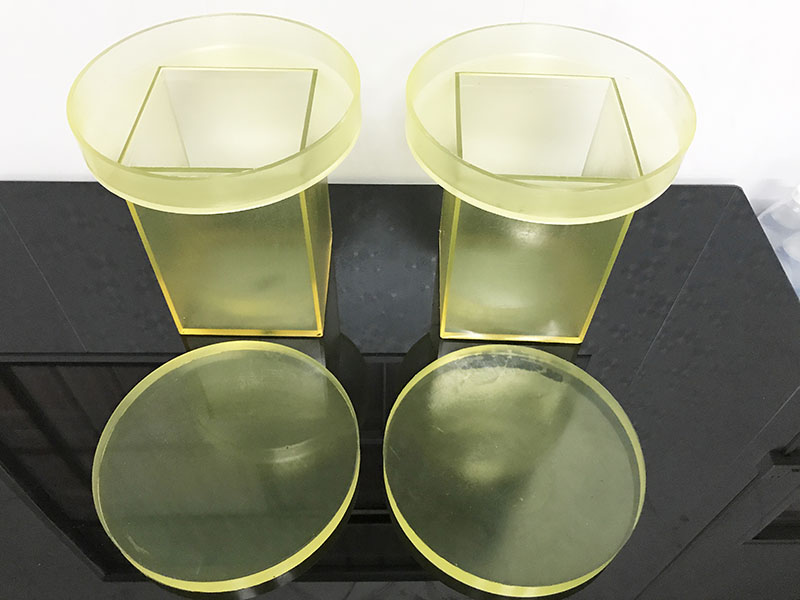
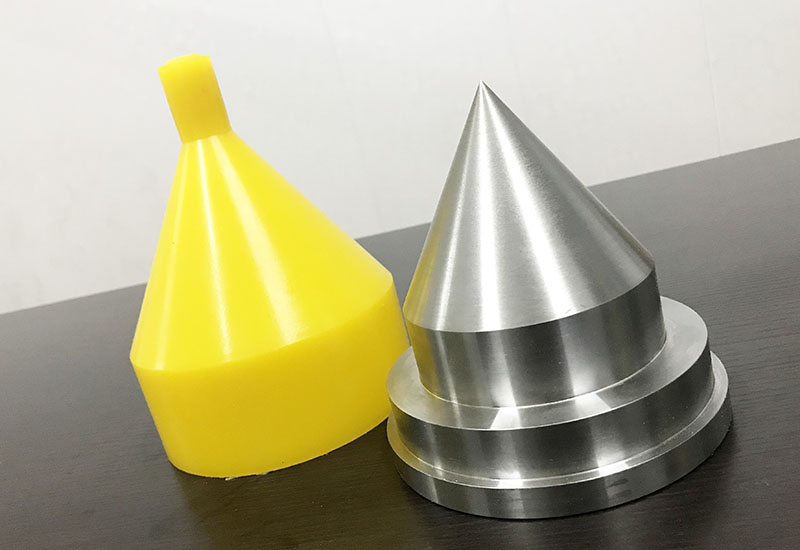
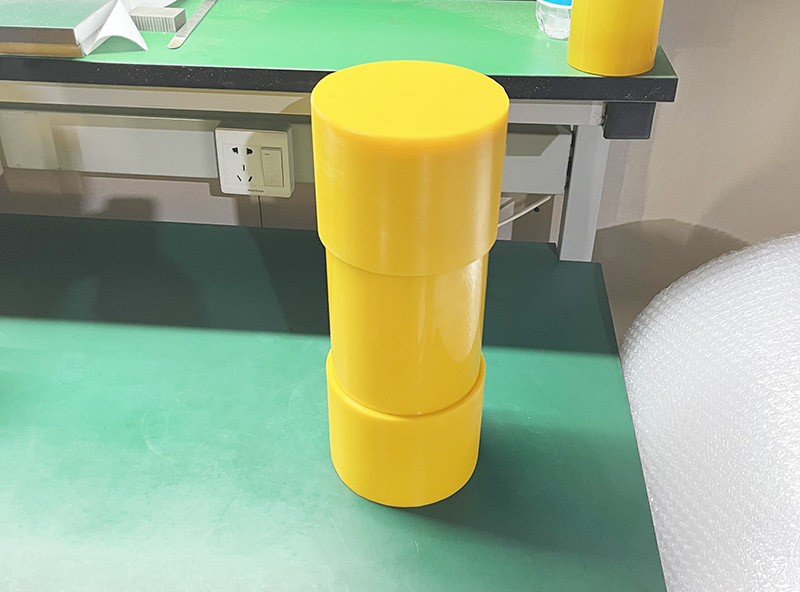