The Method of PTFE molding compression and isostatic moulding
Isostatic moulding is a method of processing PTFE powders alternative to the traditional compression and automatic moulding techniques, suitable to obtain complex shapes in a wide range of sizes.
With both, compression and isostatic moulding it is possible to produce moulded shapes from which, by mechanical machining, finishes parts are obtained.
The limit of the compression moulding is the relative geometric simplicity of the shapes that can be obtained (essentially cylindrical shapes defined by an outer diameter, an inner diameter and a height), which require considerable removal of material by means of mechanical machining when the shapes of the finished parts to be obtained are characterized by a certain complexity. And this results in high costs for the finished parts that must be obtained.
With the isostatic moulding, it is possible to obtain shapes that are very close to the geometries of the finished parts that are intended to be obtained. This means that the material to be removed by means of mechanical machining will be less and this will have a positive impact on the production costs.
Another important advantage of the isostatic moulding is that all the powder compaction phases is carried out under vacuum and this means huge qualitative benefits. The parts produced will be virtually free of porosity, giving the material superior characteristics in terms of mechanical and dielectric properties. In addition, the moulding takes place radially (from the outside to the inside or vice versa), and this gives a better uniformity of pressure transfer to the powder. The moulded part will have the same characteristics throughout its length, which is not the same achieved by compression moulding because of the friction of the powder against the mould walls.
Isostatic moulding requires the building of dedicated moulds for each geometry of the part to be realized (except for simple shapes), so it will be particularly advantageous for serial productions of at least some hundreds of pieces or more.
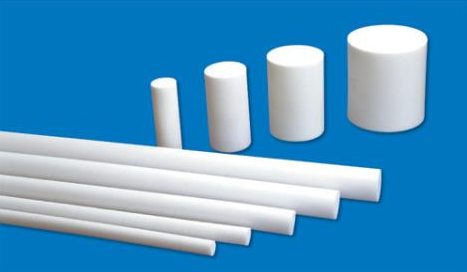
Compare to traditional rubber cold isostatic pressing bags, the polyurethane CIP bags have significant advantages. As a new polymer material, polyurethane products feature smooth surface, wearing-resistant, anti-fatigue, low deformation rate. The surface of pressed products with polyurethane bags is much smoother than that pressed with rubber bags, thus it possesses better looks and less postprocessing is required. It’s an ideal tool for powder material forming by press process, which can help a company reduce cost and increase efficiency.
Durability and deformation rate are factors that users care most. A long working life of pressing bag can reduce cost and increase production efficiency, while low deformation rate of the bag will enhance precision and yield of products. By close cooperation with material suppliers and great mass of manufacturers of carbide, ceramics and graphite products, we accumulated a lot of experience in this industry and become a well-know supplier of CIP bags.
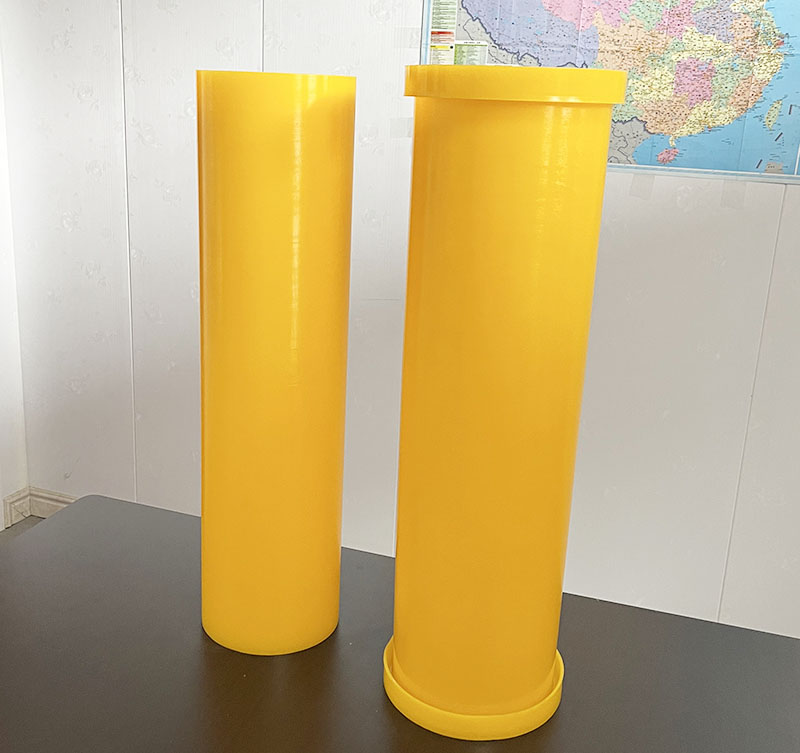
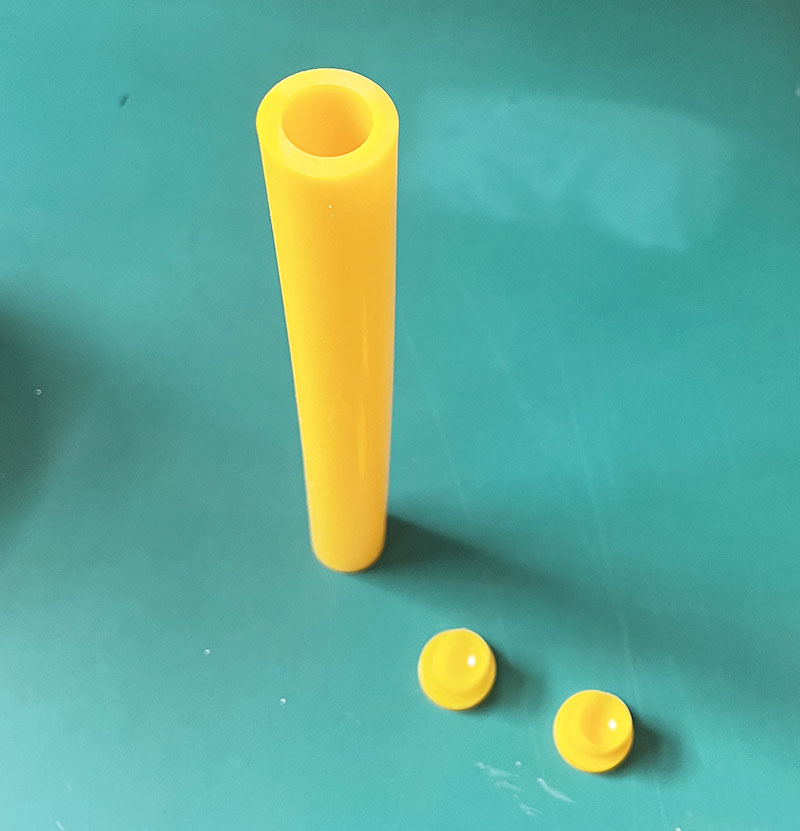
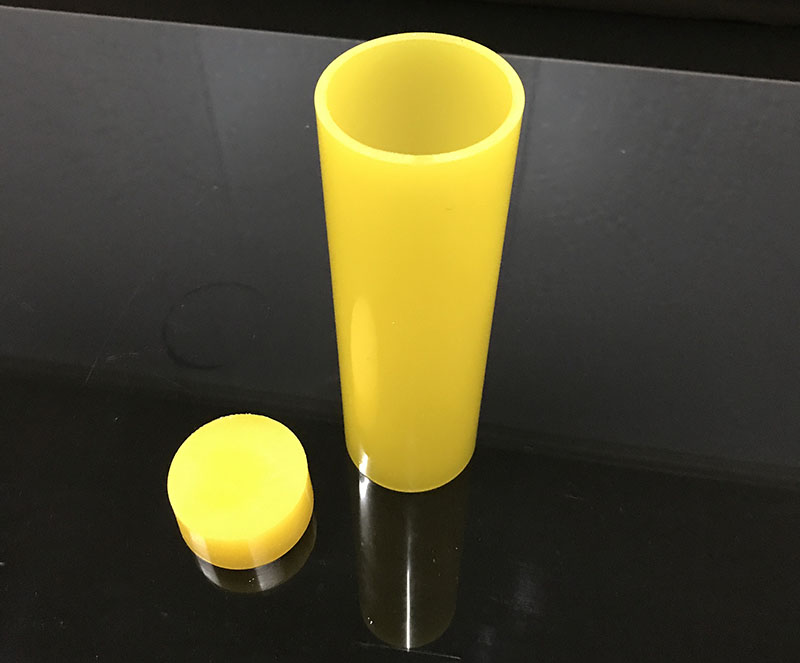
We support all kinds of customization, if you need it, please contact us.
Phone/whatsapp:+86 18234744811
Email:sales@highindustryco.com