Advantages of Cold Isostatic Pressing
Hot isostatic pressing (HIP) and cold isostatic pressing (CIP) technology has been known for more than 50 years, and is considered today to be a standard production route for many applications. As a term of comparison, Dry Pressed . CIP, Cold Isostatic Pressing, is one of material processing methods. Cold isostatic pressing (CIP) is a powder compaction technology used in materials processing engineering, and it applies the same pressure in all directions (as opposed to being reliant on the good shape matching of two at surfaces). CIP has been commonly used for processing ceramics, but not as widely used for metals. rolling, machining or sintering. The mold is placed in a pressure chamber, and high pressure is applied uniformly from all sides through a liquid medium. Cold Isostatic pressing is a manufacturing process wherein a powder is put into a bag or a sort of mold, and closed off; the bag is put into a vessel and subjected to pressure.
Cold Isostatic Pressing advantages:
· Uniform strength in all directions: The pressure used to compact the powder is applied equally in all directions.
· Uniform density: The resulting compacted piece will have uniform shrinkage during sintering or hot isostatic pressing with little or no warpage.
· Shape flexibility: Isostatic pressing makes it practical to produce shapes and dimensions that are difficult or impossible to produce by other methods.
· Component size: Wide range of component sizes can be made from massive 30 ton near net PM shapes down to densifying less than 100 gram MIM parts.
· Larger parts: Part sizes are limited only by the size of the isostatic pressure chamber.
· Low tooling cost: For short production runs, the tooling cost is low in comparison to other manufacturing methods.
· Enhance alloying possibilities: Able to enhance alloying elements without inducing segregation in the material.
· Reduced lead times: Complex shapes can be economically made from prototype to production quantities with significantly reduced lead times versus forgings or machined components.
· Material and machining costs: Near net shape parts can be fabricated, greatly reducing material and machining costs.
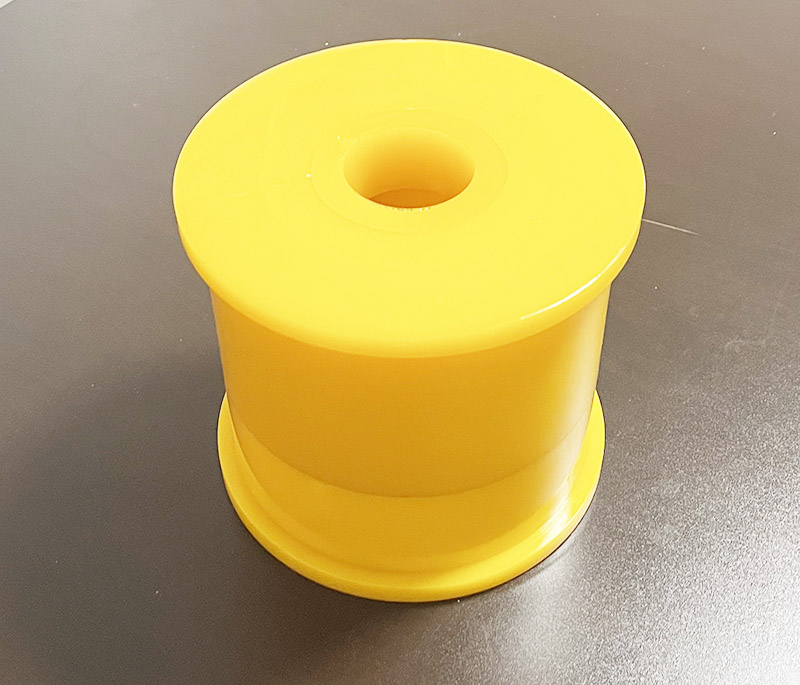
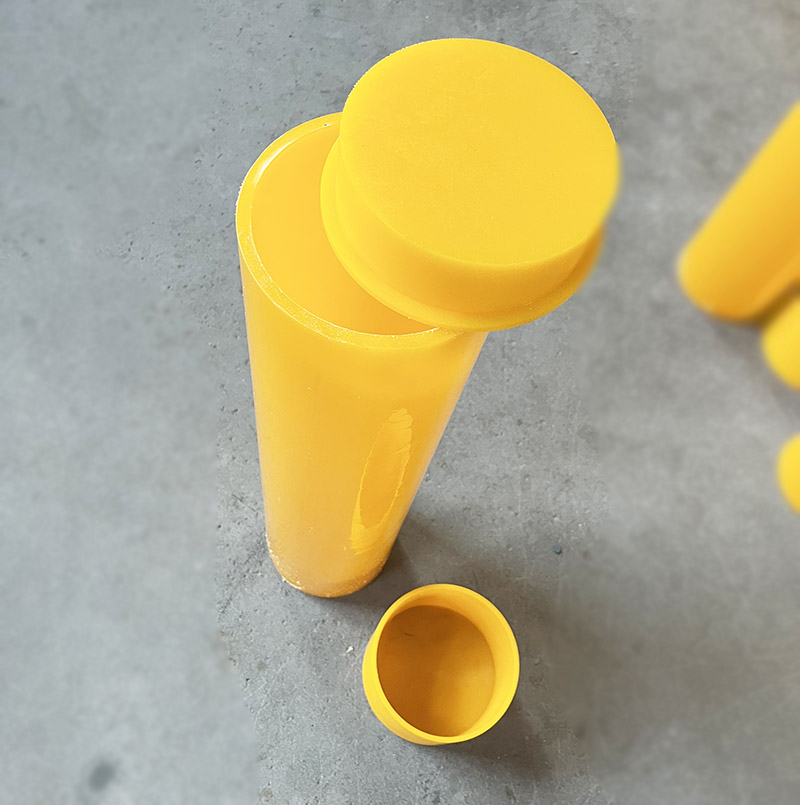
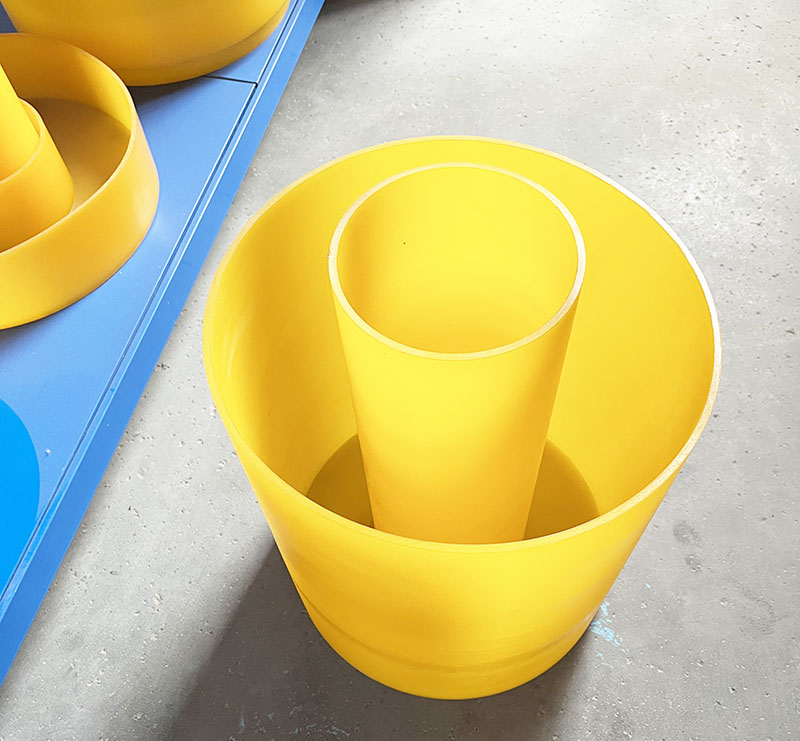
We support all kinds of customization, if you need it, please contact us.
Phone/whatsapp:+86 18234744811
Email:sales@highindustryco.com