Injection Molding
How does injection molding work?
Injection molding is to mix ceramic powder and an organic binder, and then inject the ceramic powder into the metal mold cavity at a temperature of 130~300°C through an injection molding machine. After it cools, the binder solidifies and the molded product can be taken out. Billet. Injection molding was first applied to plastic molding and metal mold casting in 1978. The process itself is characterized by strong adaptability, a short production cycle, high yield, and easy automatic control. Compared with other molding methods, injection molding can form parts with complex shapes and precise dimensions at one time, so it is widely used in the production of plastic products.
In the late 1970s to the early 1980s, with the development and development of advanced ceramic engine components. Ceramic injection molding is a new technology suitable for preparing precision ceramics. This method has many special technical and technological advantages. Compared with traditional ceramic molding technology, injection molding technology can produce structural parts with small volume, complex shapes, and high dimensional accuracy. Moreover, due to the flow die, the green body density is uniform and the sintering performance of the parts is superior. In addition, because injection molding is a near-net molding process, there is no need for subsequent processing, and the only micromachining is required, especially for silicon carbide, silicon nitride, etc., which have excellent high-temperature resistance, high strength, high hardness, and corrosion resistance The injection molding technology is particularly important in the molding method of high-temperature structural ceramics.
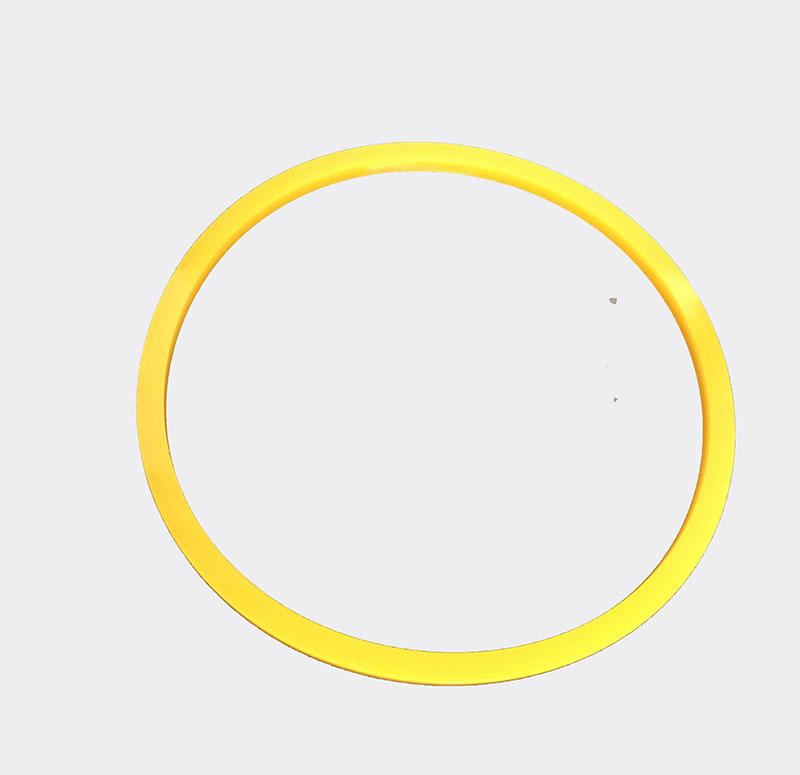
Advantages of ceramic injection molding
It has superior molding ability and can produce precision parts with complex shapes.
Because the raw materials used are finer powder particles, the primary sintering density is high, solid-phase sintering can obtain a relative theoretical density of more than 95%, while liquid sintering can reach more than 99%, and its microstructure is small and uniform, and it has excellent mechanics. performance.
The injection molding is in an isostatic state during the injection process, and the resulting molded body has a uniform density, which ensures uniform shrinkage of sintering. Therefore, the parts prepared by the injection molding method have high dimensional accuracy and small tolerances.
The product utilization rate of injection molding is high, and the sintered parts can be used without or only a small amount of subsequent processing, which reduces the production cost and can obtain higher production efficiency.
