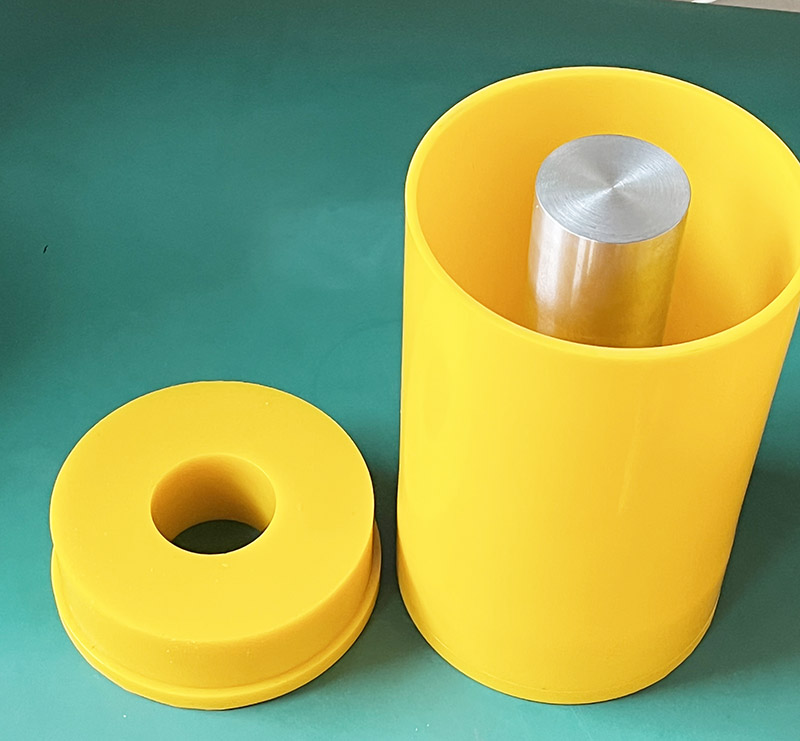
Cold Isostatic Pressing Molds for Tungsten and Molybdenum
Categories: Industry news
Application: Cold Isostatic Pressing Molds for Tungsten and Molybdenum
InquiryMain description:
Cold Isostatic Pressing Molds for Tungsten and Molybdenum
Cold Isostatic Pressing Molds for Tungsten and Molybdenum
Cold Isostatic Pressing Molds for Tungsten and Molybdenum
Cold Isostatic Pressing of Tungsten and Molybdenum
Refractory metals (mainly tungsten, molybdenum, tantalum, niobium) and their alloy materials produced by powder metallurgy. Powder metallurgy process is the main production process of refractory metals, especially tungsten and molybdenum materials.
In 1903, W. von Bolton in Germany made tantalum wire as an incandescent filament. In 1909, W.D. Coolidge of the United States used powder metallurgy to produce tungsten wire instead of tantalum wire for incandescent lamps. In 1910, the same process was used to make molybdenum wire, thus opening up the road of tungsten and molybdenum powder metallurgy. Early refractory metal products such as tungsten and molybdenum were small-sized rods, wires, foils and strips, mainly used in light bulbs and electronics industries. Since the 1940s, due to the needs of aviation, aerospace and atomic energy for high-performance, large-size refractory metal materials, vacuum smelting technology has been developed, and large-scale isostatic presses and high-temperature sintering furnaces (2400) have been developed, thus promoting the development of powder metallurgy. In the mid-1950s, China began to industrially produce tungsten and molybdenum materials required by the electric light source and electronics industry; in the late 1950s and early 1960s, tungsten-rhenium alloy wire, high specific gravity alloy and tungsten-based contact materials were developed; in the mid-1960s, large-scale cold isostatic pressing machines and high-temperature sintering furnaces were built, and a series of large-scale and high-performance tungsten and molybdenum materials and products were developed and produced.
Compared with the smelting process, the advantages of the refractory metal powder metallurgy process are: there are many types of alloys that can be produced, the alloy composition and structure are uniform, the grain size is small, the process flow is short, the energy consumption is low, and the material yield is high. However, the purity of the material produced by this method is not as high as that produced by the vacuum smelting method (the content of interstitial elements such as carbon, oxygen, nitrogen, etc. is higher), thus affecting the performance of some products.
Production process The production process of powder metallurgy tungsten and molybdenum materials includes powder production, pressing, sintering and processing. Industrially, hydrogen is used to reduce tungsten trioxide and molybdenum trioxide to produce tungsten powder and molybdenum powder. The reduction process system is mainly determined according to the powder particle size and particle size composition required for the production of powder. The higher the reduction temperature, the coarser the particle size of the obtained tungsten powder and molybdenum powder. The fine particle powder generally adopts secondary reduction: the first time is to reduce the trioxide to dioxide at a lower temperature (W550~800, Mo450~650), and the second time to reduce the dioxide to metal powder at a higher temperature (W750~900, Mo900~950). The coarser powder is produced by primary reduction, that is, the trioxide is directly reduced to metal powder at a higher temperature, or the secondary reduction temperature is increased to obtain coarse metal powder. In recent years, the process of reducing blue tungsten oxide has been developed to produce tungsten powder. The particle size of tungsten powder and molybdenum powder has an important influence on its compressibility, sinterability and final product performance.
There are two ways in the powder metallurgy industry to produce dense tungsten and molybdenum products from powder:
① Press tungsten powder or molybdenum powder into a billet with a metal mold, then vertical melting and sintering, then swivel forging, then forging rod, wire drawing or rolling into sheet; it can be used to produce small-sized wire, foil and strip.
②The tungsten powder and molybdenum powder are formed by cold isostatic pressing, and then sintered into billets or finished products. This process can produce large-sized and special-shaped parts; such as crucibles, molds, plugs and various pipes.
A Sample of Cold Isostatic Pressing Molds we made
We support all kinds of customization, if you need it, please contact us.
Phone/whatsapp:+86 18234744811
Email:sales@highindustryco.com