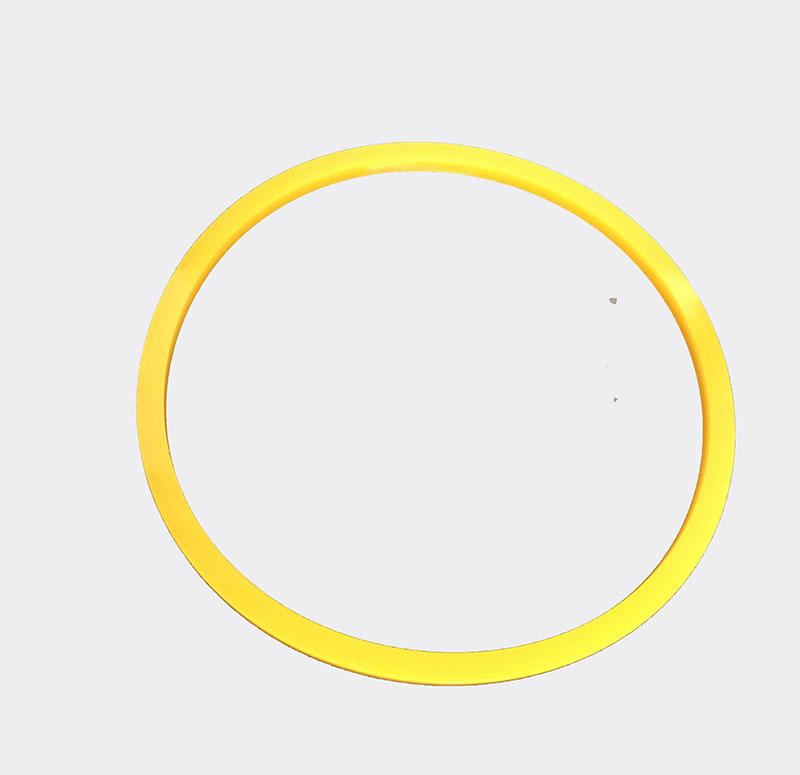
Isostatic Pressing Molds for Powder Metallurgy
Categories: Industry news
Application: Isostatic Pressing Molds for Powder Metallurgy
InquiryMain description:
Isostatic Pressing Molds for Powder Metallurgy
Isostatic Pressing Molds for Powder Metallurgy
Isostatic Pressing Molds for Powder Metallurgy
With the continuous improvement of the level of science and technology, the traditional powder metallurgy technology is gradually difficult to keep up with the requirements of the industry, and the entire metal industry is in a sluggish state. Isostatic pressing technology is a new material forming method that has emerged along with technological progress. It is an innovation of traditional powder metallurgy technology. Applying it to powder metallurgy will greatly shorten the time of material production and improve the yield of powder materials. Production efficiency and quality.
Basic concept of isostatic pressing technology
Isostatic pressing technology is simply a technology that applies equal pressure to the surface-closed material from all directions. In powder metallurgy, this technology is mainly used for the consolidation and molding of powder materials. According to practice, the application of isostatic pressing technology in powder metallurgy has obvious technical advantages. First, this uniform pressure can make powder metallurgy materials denser and make them have higher strength; secondly, isostatic pressing technology can Reduce or even eliminate defects within materials; finally, this technology can also function as an adhesive, bonding dissimilar materials together at high temperatures. Due to the obvious advantages of isostatic pressing technology in the field of powder metallurgy, this technology has been widely used in the field of materials science and engineering. So far, products processed by isostatic pressing technology have been applied to industries with severe material requirements such as aerospace, mining machinery, artificial diamond, petrochemical and atomic energy. Under certain conditions, isostatic pressing technology can directly form alloy parts with geometric structure load, and the products produced by isostatic pressing powder metallurgy technology have better physical and mechanical properties. The application of isostatic pressing technology enables some powder metallurgy material products to replace casting metallurgical materials in terms of performance and service life, thereby reducing the use of casting technology and having a certain environmental protection effect.
Classification of isostatic pressing technology
Isostatic pressing technology is classified according to different heat consumption and use characteristics, and is divided into hot isostatic pressing, warm isostatic pressing and cold isostatic pressing. The packaging mold materials, pressure medium materials and corresponding applications of these three technologies Devices are all different.
Cold isostatic pressing
The static pressure technology is carried out at room temperature. The mold and material of the sheath are generally plastic or rubber, and certain substances are also required as the pressure medium. The elastic substances include rubber and plastic, and the inelastic substances include liquid. The substance called water isostatic pressing in cold isostatic pressing generally uses rust remover as the water medium, and oil isostatic pressing uses oil as the pressure medium. In addition, thick-wall molding or soft molding uses elastic materials to maintain balance. The preformed blank is formed by means of hot isostatic pressing or forging, and the final form of pressing is sintering.
Warm isostatic pressing
The temperature of the warm isostatic pressing device is required. The lower temperature is 80°C, and the higher temperature is 120°C. It is also possible for a slightly higher temperature. The highest temperature can reach 450°C, but under normal circumstances the temperature is 250°C. ℃, the transmission medium is generally set to oil. It should be noted that the control of the cooling process and the heating process needs to be set according to the process requirements to determine whether it will generate heat. The condition is that it is in a high-pressure cylinder and the temperature must be controlled in the cylinder. For heating measures, the oil tank is a relatively common heating tool. The choice of transfer medium is also important, usually choose the wet bag static press and equipment similar, and sometimes choose warm isostatic pressing, because the powder is difficult to form, and at room temperature, the forming conditions are There are many, choosing warm isostatic pressing is the best choice.
Hot isostatic pressing
Affected by the process of static pressing, the control of materials is greatly affected, and because the external conditions affected are high pressure and high temperature, when eliminating casting defects, two methods of bonding and diffusion will be selected as much as possible. Pressure The choice of transmission medium is generally inert gas. In another special case, it can be selected as the transmission medium for hot isostatic pressing, such as solid particles and liquid metal. When preparing glass and metal, the sheath is often The encapsulated material to be pressed will be selected. At this time, the main function of the static pressure device is to balance.
Effect of Isostatic Pressing Technology on Production of Powder Metallurgy Materials
The application of isostatic pressing technology in the production of powder metallurgy materials is mainly manifested in the forming process of powder materials. Its specific role in production and its impact on material properties are mainly summarized as the following three points:
Influence on the forming process
Isostatic pressing technology is mainly divided into cold isostatic pressing technology and hot isostatic pressing technology. When pressing with cold isostatic pressing technology, the powder will be subjected to uniform force of the same strength in all directions. During the pressing process, the powder and There will be no large friction between the equipment, so the metal powder formed by the cold isostatic pressing technology is about 10% higher than the material pressed by the traditional pressing method, and the distribution of the green compact density is also more uniform, which is conducive to the preparation Forming products with complex structures and fine craftsmanship.
With the continuous advancement of science and technology and the improvement of the world's industrialization level, powder metallurgy technology has also achieved considerable development under the premise of resource and energy shortages. Applying isostatic pressing technology to powder metallurgy is a great attempt in the field of smelting, and to some extent it can be said to be a beneficial change in powder metallurgy technology. The wide application of isostatic pressing technology in the production of powder metallurgy materials can not only increase the utilization rate of materials, but also reduce the surface defects and internal stress of materials, improve the physical strength and mechanical properties of materials, and have great significance for the further development of powder metallurgy products. positive meaning.
We support all kinds of customization, if you need it, please contact us.
Phone/whatsapp:+86 18234744811
Email:sales@highindustryco.com